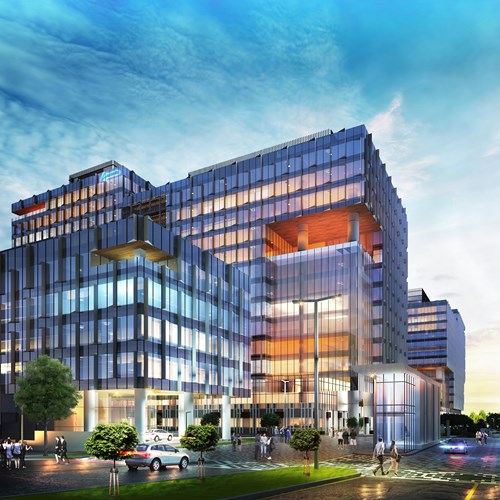
This article is contributed by Mr Rakesh Morudkar, Managing Director, RSM Facade Solutions
The project is no less an engineering feat as it is a design one.
The Facade Consultant -
RSM Design Solutions, the brain child of Mr Rakesh Morudkar is a facade engineering firm with a gamut of designers, engineers and structural engineers with operations spanning the Indian subcontinent.
In tune with their mission to provide sustainable performing cost effective building envelopes addressing latest developments in the façade technology, raising quality standards, setting new bench marks in the façade designing and engineering sphere, Mr Morudkar embarked upon the journey to make the architect's vision an engineering marvel.
The Engineering -
The architects - DSP Architects and Associates came up with a novel and innovative concept of a functional design for Sun Shading – a specially engineered fin which is 500 mm wide and 20 mm thick.
In order to turn this Concept to realty, RSM Design Solutions began to engineer the solution in line with their policy of zero/negligible deviation from design intent. Thus, designs, alternative designs, calculations , analysis, heat gain studies and heat dissipation calculations etc. were done in ECO tech.
Considering the property’s long life span it was proposed to go for reputed and tested façade system complying with local and internal regulations and the performance requirements
The system used for this project is a gasket based split unitised system from Technal – GEODE EL with following advantages -
Having studied the architect intent, the façade consultants - RSM Design Solutions, did a thorough thermal analysis, a standard practice for the system and the same was repeated with the add on Fin. It was conceptualised to install Fin at a distance from the façade line with help of specially designed brackets which were placed strategically not to hinder Openable windows, ease of replacability of glass and at Stack Joints etc. The main function being no heat transmission from Fin to the system.
Further RSM proposed to use same Technal system without any modification at VRV location. Mesh and glass line was kept the same and not staggered, thus eliminating additional hardware, brackets and labour for installation and in turn the total Project Cost.
As the design of façade had a cantilever of 3 meters, RSM designed the system considering the above and the relevant values were proposed.
The Façade also had another combination – At refuge area the termination of two corners was at 90 Degree where the façade needed to extend. The details proposed by RSM were correctly replicated without any deviation by Technal – refer Figure i
FIGURE I – REFUGE AREA CORNER DETAILS
The fins were designed considering ergonomics, aesthetics, functionality and repeatability and followed the below mentioned standars -
The ‘Counter Sunk bolt’ was also designed to be flush with the fin surface and not jetting out.
Manufacturing aspect:
The fin could be manufactured in two ways - Aluminium Sheet bending and Aluminium Profile Extrusions, both which pros and cons were weighed at length -
ALUMINIUM SHEET BENDING
Advantage
Disadvantages
ALUMINIUM PROFILE EXTRUSION :
Advantages:
Disadvantage
As the advantages of extruded fins outweighed those of fins made of sheet aluminium, Extruded profile fins were chosen.
Design and Engineering of Fins
Total number of fins for the Project is approximately 1800.
1. Design Consideration -
2. Ergonomics and Cost aspects -
Fin assembly and fixing
The horizontal Fin element was joined at 90 degrees to vertical part using corner cleat which was welded at the intersection.
Fin fixing is detailed in following illustrations
Performance Mock-Up Test
A PMU test was carried out for the Technal system with the Fin Element and it passed all the tests successfully and with ease at the 1st go.
The test was carried out at Façade India Testing Laboratory, Murbad.
Further the Fin also Successful passed the Push and Pull test carried out separately after , the PMU test.
The PMU was seamlessly executed by Glazium Facades Pvt Ltd and the project is now under execution at tremendous pace by Glazium Facades Pvt Ltd.
Glazium Facades Pvt Ltd, a leading facade specialist, boasts a 500+ member strong team, with over 10 years of experience and 5,00,000+ square meters of facade works completed.
Technal India was proud to collaborate with Glazium Facades Pvt Ltd for this iconic project.